Operating Properties of the NM200UW
Nuclear Underwater Laser Scanner
Precise, Reliable and Efficient In-Vessel Dimensioning
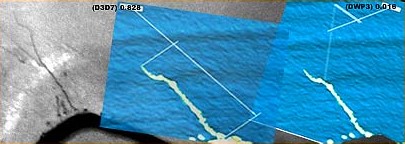
In-air laser scanners have existed for several years, but precise underwater laser scanning is much more challenging, especially within PWRs and BWRs. Newton-developed software makes underwater laser scanning possible in this environment by compensating for water turbulence, heat and radiation while producing a point cloud of great detail and density.
Nuclear plant operators need precise measurements of as-built components located in-vessel and in the pools, or other underwater plant locations, that need to be inspected in order to track cycle-to-cycle degradation and to obtain measurements of components in order to achieve a correct fit for fabricated replacement parts.
Operational Characteristics
- The NM200UW operates by laser triangulation. The projected laser line sweeps the target surface and the high resolution camera, centered on the target, captures and records any deformation of the line as a point cloud, enabling ultimate 3-D computation.
- The NM200UW is able to scan a target as close as 6 in. (150mm) and out to a distance of 3 ft. (0.9M) for a scan coverage area of 2.1 ft. x 2.9 ft. (64 cm x 88 cm).
- The NM200UW is designed to scan and capture much larger target areas by combining several point clouds together to form larger composites.
- Operators may select from several levels of scan quality via the user interface. The shortest, most coarse scan takes 15 seconds, while the longest and most detailed takes approximately three minutes.
- Laser light color is maximized for water penetration. The specific wavelength of the laser allows for highest possible efficiency underwater transmission.
- The scanner camera only accepts the specific color produced by its own laser and LED lights, greatly reducing any contamination from stray light in the scanning environment; thus making the NM200UW relatively immune from any other underwater work lights during operation.
- The system measures underwater targets to an accuracy of +/-.0004 (0.01mm).
- In the visual observation mode, the high-intensity LED ring array on the head illuminates the area and the high-definition camera transmits a monochrome image to the control console screen to assist the operator for optimum positioning and on-site analysis.
- The control console powers and communicates with the scanner through the cable via low-voltage DC power and signals, and the camera sends scan results up via Gigabit Ethernet.
- All data is permanently stored for later analysis and study.
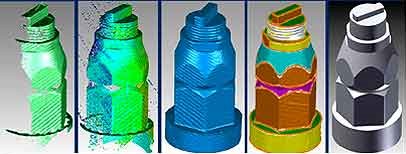